Problem
Textile industry is complex in nature.
- Air jet Looms & Winding Machines are major consumers.
- Negligence in machine specification selection- uncertain compressed air demand
- In Composite textiles – Synchronization is a big challenge for high & low pressure.
- Existing Vortex & Orifice flowmeters unable to record low flowrate consumption.
- Have high pressure drop upto 3 psig which creates an energy loss.
- Unable to identify compressed air leakage in various departments.
Solution
Leomi – 586 Insertion Thermal Mass flowmeter
- Doesn’t require shutdown for installation
- High turndown down ratio of 100:1
- No pressure drop against existing flow meter installed saves energy cost
- Allows leakage detection with better accuracy
- No maintenance than the existing flow meter used.
Application
Compressed air consumption monitoring and recording in air jet Looms & Winding machines.
Customer
World’s biggest Textile plant, Gujarat
Product
LEOMI- 586, Insertion Thermal Mass Flowmeter
Why Leomi?
- An ISO 9001:2015 company, Startup India recognized
- German technical collaboration Engineered in India
- India’s First In-house fully automatic wind tunnel calibration system
- Product quality proven for more than 20 years installed worldwide.
Installation Facts
Leomi 586 is installed in the main branch of the different departments on 12” (DN300) pipe with 6000 SCFM flow rate with isolation ball valve providing easy removal. They are monitoring more than 150 Airjet looms and winding machines and have been used by customer for more than 3 years. Solved consumption problems of different departments. Payback in less than 6 months.
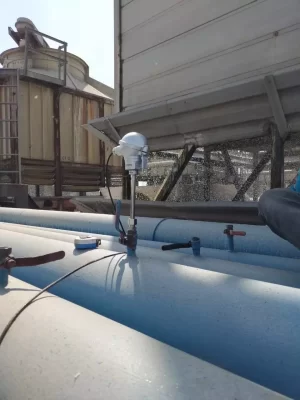
Download the Complete Case Study